Enjoy exclusive quality on premium brushes!
The Essential Role of FRP Brushes in the Chemical and Petrochemical Industry
The chemical and petrochemical industry operates in some of the harshest environments, with exposure to corrosive chemicals, extreme temperatures, and hazardous substances. Equipment maintenance is crucial to ensure safety, efficiency, and longevity. One of the most effective tools in industrial cleaning and maintenance is the FRP (Fiber Reinforced Plastic) brush. These brushes provide a durable, non-corrosive, and safe solution for cleaning and maintaining critical infrastructure, including storage tanks, pipelines, and processing equipment.
FRP FIBERGLASS BRUSH
ASHA BRUSH PRODUCT
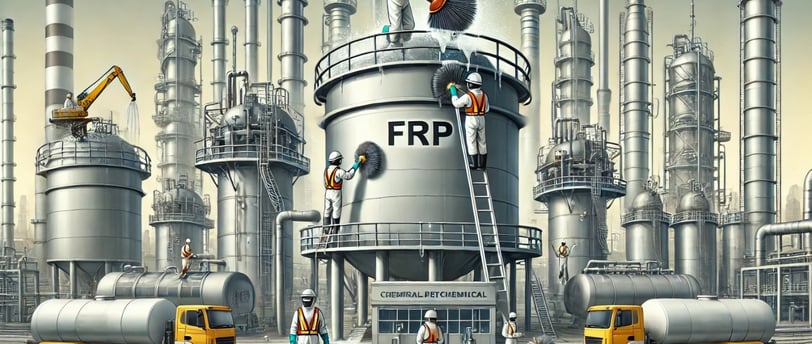
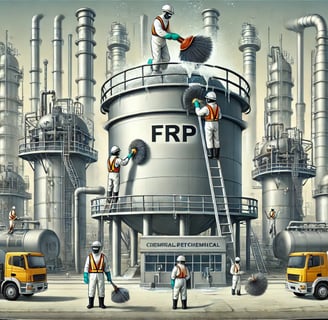
What is an FRP Brush?
FRP brushes are made from fiber-reinforced plastic, a material known for its lightweight strength, corrosion resistance, and non-conductive properties. Unlike metal brushes, FRP brushes do not rust or degrade when exposed to harsh chemicals, making them an ideal choice for use in chemical plants, refineries, and petrochemical facilities.
Uses of FRP Brushes in the Chemical and Petrochemical Industry
1. Cleaning and Maintaining Storage Tanks
Storage tanks used in chemical plants and refineries accumulate chemical residues, sludge, and contaminants over time. FRP brushes help in scrubbing off stubborn deposits without damaging the protective lining of tanks, ensuring their structural integrity.
2. Removing Corrosion and Scale from Pipelines
Pipelines transporting chemicals and petroleum products often develop scale, rust, and chemical buildup that can lead to clogs and efficiency loss. FRP brushes provide an effective solution for cleaning pipes without causing sparks or corrosion, making them safe for hazardous environments.
3. Cleaning Processing Equipment and Machinery
Chemical processing units, reactors, and distillation columns require regular cleaning to prevent cross-contamination and system inefficiencies. FRP brushes help remove chemical residues, hardened deposits, and grease, ensuring smooth operation and compliance with safety standards.
4. Surface Preparation for Coatings and Repairs
Before applying protective coatings or making structural repairs, surfaces need to be cleaned thoroughly. FRP brushes help in removing dust, debris, and old coatings from metal and concrete surfaces, ensuring better adhesion and durability of new coatings.
5. Decontamination of Work Areas and Spill Cleanup
In the event of chemical spills or leaks, FRP brushes assist in decontaminating surfaces, helping to prevent workplace hazards and environmental contamination. Their chemical resistance makes them ideal for handling hazardous cleaning tasks.
Advantages of Using FRP Brushes in the Chemical and Petrochemical Industry
✔ Corrosion-Resistant: Unlike metal brushes, FRP brushes do not react with chemicals or rust over time.
✔ Durable and Long-Lasting: Built to withstand extreme industrial conditions, reducing replacement frequency.
✔ Non-Sparking and Safe: Ideal for hazardous environments where flammable substances are present.
✔ Non-Conductive: Provides electrical safety when used near energized equipment.
✔ Eco-Friendly: Reduces the need for aggressive chemical cleaners by effectively scrubbing surfaces.
Conclusion
FRP brushes play an essential role in cleaning, maintaining, and ensuring safety in the chemical and petrochemical industry. Their durability, resistance to corrosion, and non-sparking properties make them an invaluable tool for industrial maintenance teams. By integrating FRP brushes into regular cleaning and maintenance routines, companies can improve equipment lifespan, workplace safety, and operational efficiency while reducing downtime and costs.
For industries handling hazardous chemicals and petroleum products, FRP brushes offer a safe, reliable, and efficient cleaning solution that meets the demands of modern industrial maintenance.